【やさしく解説】リーンシックスシグマでムダとムラを改善。活用事例や成果を紹介!
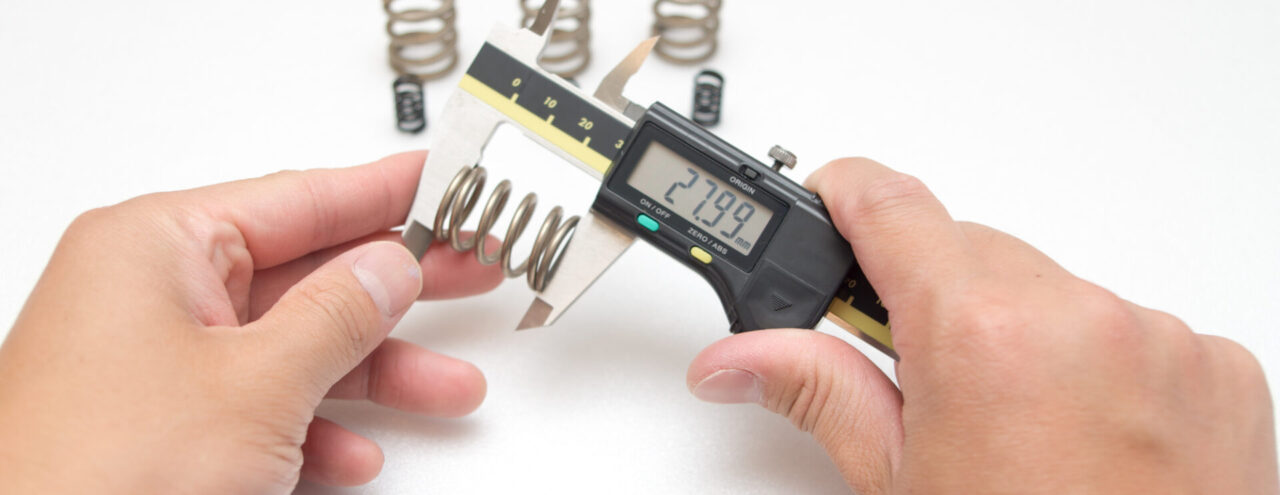
この記事のまとめ
・リーンとは「ムダの改善」でトヨタ自動車の生産手法がその起源である
・シックスシグマとは「ムラの改善」で、本来は「100万個(回)のうちの不良(ミス)を3.4個(回)に抑えること」を意味し、不良を限りなく0に近づけることである
・リーンシックスシグマは改善根拠を可能な限り数値化された客観的データとしているため、改善
において社員の合意を得やすい
・リーンシックスシグマとはムダとムラを改善し、安定して求める成果を出すことである
目次
リーンシックスシグマとは「ムダ」と「ムラ」をなくすこと
リーンシックスシグマとは?
リーンシックスシグマ(Lean Six Sigma/略称:LSS)とは、ムダとムラを排除して業務効率化を図ることです。リーンシックスシグマは、マーケティング用語である「データドリブン」という、情報を可視化して定性的な部分も可能な限り数値化し、数字を業務改善や課題解決の根拠とする点が特徴です。「感覚的にこうすればいい」「経験的にこうすると成功する」といった感覚や経験値による意思決定ではなく、数値にすることで説得力が生まれます。
リーンシックスシグマは造語
リーンシックスシグマ(Lean Six Sigma)とは、「数字を根拠として、ムダとムラを排除し業務効率化を図ること」と説明しました。そもそもリーンシックスシグマは、「リーン(Lean)」と「シックス(Six)」と「シグマ(Sigma)」を合わせた造語ですが、LSSをもう少し詳しく解説するためにそれぞれの単語に分解して説明します。
単語 | 英語表記 | 意味 |
リーン | Lean | 贅肉のない、引き締まっている |
シックス | Six | 6、6つ |
シグマ | Sigma | 標準偏差(※) |
※標準偏差とは?
データのバラツキ具合を示し、標準偏差0はバラツキがないことを示します。すなわち標準偏差の数字が低いほど、バラツキが少ないことを意味します。
これらを整理すると、「贅肉のない、6、バラツキ」となります。難解な日本語になりましたが、これらについて次のトピックスからそれぞれ詳しく、わかりやすく説明します。
リーン=贅肉がないこと
こちらでは、まず「リーン」について紹介します。
リーンとは「贅肉のない」こと
リーンは前項で紹介した通り、「贅肉のないこと」すなわち「無駄(ムダ)がないこと」を意味するのですが、そもそもリーンとはリーン生産方式という生産方式の名前であり、日本のトヨタ自動車の生産方式を米国のマサチューセッツ工科大学の教授が体系化したもので、トヨタ生産方式とほぼ同じ意味です。
リーン生産方式とは?
1980年代に、日本車の低価格・高品質に対して政府や北米の自動車業界は、ダンピング(不当に安くして売り、シェアを獲得すること)だと批判しましたが、アメリカの有名大学であるマサチューセッツ工科大学(MIT)の教授は、日本車(トヨタ自動車)の競争力の原点として、ムダを排除する経営手法に着目し、研究をはじめました。
トヨタ自動車のムダを排除する生産工程は、トヨタ生産方式(かんばん方式)と呼ばれ、生産の各工程で必要な部品を、必要な時に、必要な量だけ供給することで、在庫を圧縮し、経費を減らす生産技術を指します。この生産技術を体系化したリーン生産方式の「リーン」がリーンシックスシグマの語源で、ビジネスでは世界中の製造業を中心に取り入れられている業務効率化の手法です。
シックス=6、シグマ(σ)=バラツキ
次に、「シックスシグマ」について紹介します。こちらはリーンと比べてやや複雑なので、具体例を用いてわかりやすく説明します。
「シグマ(σ)」とは標準偏差のこと
シグマとは標準偏差を意味します。この標準偏差とはデータのバラツキの度合いを示します。しかし、「標準偏差=データのバラツキ」と言われてもピンとこないですよね。データのバラツキとは何でしょうか?
「標準偏差=データのバラツキ」とは?
標準偏差について具体例を用いて確認しましょう。以下は小学生5人の国語のテスト結果をまとめた表です。
リスト(名前) | 国語のテスト得点 |
Aさん | 90点 |
Bさん | 80点 |
Cさん | 40点 |
Dさん | 60点 |
Eさん | 90点 |
出典:株式会社AVILEN 標準偏差の意味と求め方
この5人の平均点は、(90点+80点+40点+60点+90点)÷ 5名=72点となります。
一方で、標準偏差は以下の計算式により算出します。
①各リストにおいて、「(得点−平均点)の2乗」を算出して足し合わせる
②①を「リストの数」で割る
③②の平方根をとる
よって、今回の5名のテストの標準偏差は以下の計算式になります。
①(90-72)*2乗+(80-72)*2乗+(40-72)*2乗+(60-72)*2乗+(90-72)*2乗=1,880
②1,880÷5 = 376
③√376=約19
この約「19」が標準偏差となります。
この「19」が持つ意味は、「平均点±19の中に、大体の人がいる」ということです。
正規分布グラフにおける標準偏差が示す範囲
出典:株式会社産業革新研究所 ものづくりドットコム 正規分布について
上の表のμは平均値です。この平均値に対して、±σ(シグマ)の間に約68.27%、±2σの間に約95.45%、±3σの間に約99.73%のデータが含まれることを意味します。
今回の国語のテストはリストが5名と少ないですが、基本的な考え方として、5名の平均点が72点で標準偏差(σ)が19なので、53点から91点の間に68.27%の生徒が入る確率が高いことを示しています。
シックスシグマは何を意味するのか?
先ほどの正規分布に補正を加えた上で、各シグマの範囲から外れるものをエラーと考えると、そのエラー数は以下の通りとなります。
シグマレベル | 100万個生産あたりのエラー件数 |
1(σ) | 690,000 |
2(2σ) | 308,537 |
3(3σ) | 66,807 |
4(4σ) | 6,210 |
5(5σ) | 233 |
6(6σ) | 3.4 |
出典:SBクリエイティブ株式会社 シックスシグマとは何か? 事例や図解で解説する、GEらを成功に導いた経営手法の基礎
シックスシグマとは、100万個の製品を生産した際に、エラー件数(不良製品)が約3.4個であることを意味します。この言葉は、アメリカの通信機器メーカーであるモトローラ社が開発した商品の品質管理(経営管理)の手法であり、日本企業で実施されていた品質管理活動であるQC(Quality Control)サークルを参考にしたと言われています。
現在では製造現場における商品の品質管理に留まらず、様々なミスや欠陥の発生率を100万分の3.4の範囲に抑えることを目標に、継続的に改善を重ねていく活動を示します。
なお、2011年には、ISO(国際標準化機構)が経営改善手法の国際規格の一つとして、ISO13053(プロセス改善における定量的方法。2015年にはISO18404の認証規格を制定)にシックスシグマを採用し、のちにISO9001(品質マネジメントシステム)の認定にあたり、シックスシグマの活用を推奨しています。
ポイントは定義、測定、分析、改善、管理の5つ
ここまで、リーンシックスシグマの意味について詳しく説明しましたが、「ムダやムラを排除する」成果を得るために、どのよう活用すればいいのでしょうか。実は、リーンシックスシグマで改善を図る際にはいくつかのフレームワークがあり、その1つをDMAIC(ディーマイク)といいます。
DMAICは以下の言葉の頭文字をとったフレームワーク(方法論)です。
DMAICの構成要素
DMAICの構成要素 | 内容 |
Define(定義) | 取り組むべき課題と目標を「定義」する |
Measure(測定) | 現状を「測定」する |
Analyze(分析) | 原因を「分析」する |
Improve(改善) |
「改善」策を検討し、実行する |
Control(管理) | 定着に向けて「管理」する |
DMAICはPDCAと似たフレームですが、PDCAに比べて課題の定義、測定、分析(D、M、A)に重きを置いていることが特徴です。つまり、PDCAでいうPlanをより細分化しています。さらに、リーンシックスシグマをこのフレームワークに沿って実行する組織の中のチームも決まっており、その役職と役割を紹介します。
リーンシックスシグマを実践するチームの役職と役割
役職名 | 役割 |
チャンピオン/スポンサー | 責任者。オーナーとして結果に責任を負う |
マスターブラックベルト | 指導者。全体の活動の推進役を担う |
ブラックベルト | シックスシグマ専任のチームリーダー |
グリーンベルト | 通常業務と兼任のチームリーダー |
イエローベルト | 通常業務と兼任のチームメンバー |
シックスシグマを導入した企業では、上記の役職名と役割が決められます。これは全世界共通の役職名と役割で、「あるプロジェクトでブラックベルトを担い、相応の成果を出した」ということを、異業界、異企業でも評価されることが欧米を中心に多々あります。
特に、ブラックベルトはイギリスや中国などでは国家資格となっているほどで、日本では国家資格ではないものの、ブラックベルトやグリーンベルトなどコースや難易度に応じた研修やセミナーを取り入れている会社が多く存在します。
具体例で理解するリーンシックスシグマの活用と成果
リーンシックスシグマの活用と成果の具体例
ここでは、ガソリン噴射機の燃焼効率のバラツキ改善という、実際のものづくり現場での品質向上を目的に、リーンシックスシグマのフレームワークの1つであるDMAICの5つのステップを用いて成果を出した事例を簡易化し、数字を修正した形で紹介します。
Define(定義)
ガソリン噴射機において、ガソリン噴射後の燃焼効率にバラツキが起こるという問題が生じていました。いずれも製品のスペック規格内ではあるものの、燃焼効率が高い製品群(便宜上、正規品と定義)と低い製品群を対象に比較調査をしたところ、燃焼効率が低い製品は相対的に噴射圧が低い傾向があることがわかりました。そして、この噴射圧のバラツキの改善を「取り組むべき課題」として社内で定義し、課題解決へ向けて改善対応することになりました。
Measure(測定)
無作為に1万本のガソリン噴射機を確認したところ、そのうち0.3%の製品の噴射圧が正規品に対して低いことを確認しました。あわせて、噴射圧が低い製品はいずれも燃焼効率が平均値よりも低いことを再度確認しました。正規品と噴射圧が低い製品において、部品仕入れ先、部品納入日、組立て日、組み立てライン、保管方法の違い等を確認しつつ、製品寸法などのスペックも含めて「測定」しました。
Analyze(分析)
噴射圧が低い製品のうち95%の噴射穴は、中心から約0.01mmを超えて0.02mm以内のズレがあることがわかりました。一方で、正規品のうち97%の噴射穴は、中心から約0.01mm以内に収まっていました。その他にもいくつかの差異が認められましたが、もっとも有意差のある差異が噴射穴の位置だったため、穴あけ加工に主因があると「分析」しました。さらに、噴射圧が低い製品はすべて、複数ある製造ラインのうち特定のラインで製造されていることもわかりました。
Improve(改善)
噴射穴を開ける工程において、噴射圧の弱い製品を製造したラインの穴あけ機は、他のラインの穴あけ機よりも、穴あけ時における製品の固定圧力がやや弱いことがわかりました。いずれも規格内でしたが、圧力を他のラインと同等に設定を調整したことで、穴の位置が中心から0.01mmの範囲に収まることを確認しました。
改良後の穴あけ機によって加工された製品をレビューすると、99%の製品の穴が中心から0.01mm以内に収まるようになり、噴射圧もほぼ正規品と同レベルになりました。ラインを改善したのちに、再度無作為に1万本の製品を確認したところ、噴射圧が低い割合が改善前の0.3%から約0.01%に減少し、製品の質が「改善」されました。
Control(管理)
作業マニュアル上、噴射穴の位置は中心値±0.03mmまで許容していましたが、これを±0.01mmに規格変更し、製造ラインのチェック項目にある「穴あけ機の固定圧力」の規定も変更しました。加えて、品質保証の作業マニュアルにも噴射穴の許容位置の変更を反映し、製造ラインの「管理」に至りました。
※以上の内容は、実際に製造業で生産技術に従事する社員の実経験をもとに作成しておりますが、秘密保護の観点と説明における便宜上の観点から、実際の数字を含めて事実とは異なる内容に一部変更しております。
今回は具体例をテキスト形式で紹介しましたが、実際の現場ではこのような改善の実行にあたり、バリューストリームマップ(VSM)を作成しましょう。VSMを使用することで商品の資材と情報の流れを明確に可視化されますので、フェーズごとの分析や改善が効率よく実現できます。そして、工程ごとのムダやムラの削減にもつながります。
リーンシックスシグマの副次的効果
このように業務プロセスの改善がリーンシックスシグマの目的ですが、副次的な効果として人材育成や社員のモチベーションアップも期待できます。リーンシックスシグマは体系的な分析に加え、効果の最大化を実現するために各改善の重要度を定量的に判断し、優先順位を決定しますので、具体的に以下の効果が期待できます。
- 定量データに基づいて意思決定をすることで、「経営視点」を養うことができる
- プロジェクト推進に際し、関係者を巻き込み、「チームを機能させるノウハウ」を学習できる
- 上記2つを含め、社員の「スキルや経験、モチベーションをアップ」させることができる
また、個人の感覚やアイデアによって改善がなされるのではなく、データドリブンでもって実行することで異論の余地が少ない客観的なデータに基づいて判断が下されますので、トップダウン的な側面が強いリーンシックスシグマではありますが、社員のモチベーションがダウンするリスクは低く、たとえボトムアップの社風を持つ企業でも、押しつけ感なく改善活動が受け入れられる傾向があります。
まとめ
今回は、リーンシックスシグマについて、その概要や活用方法等についてわかりやすく紹介しました。製品やサービスの品質管理の改善や向上は、購入や利用するすべての顧客に同じ価値を提供することができますので、ぜひリーンシックスシグマを活用して顧客満足度を高めましょう。また、従業員の業務効率化におけるスキルアップにも効果を発揮することも紹介しましたので、人材育成にも役立てましょう。
ベネフィット・ワンでは、データ活用プラットフォーム「ベネワン・プラットフォーム」を提供しています。ベネワン・プラットフォームは、社内に点在する従業員の人事データを一ヶ所へ集約し、一元管理するツールです。そして、集約されたデータは可視化してデータ同士の相関分析することで、従業員1人ひとりの「個」のマネジメントが可能になります。人事の業務効率化や業務改善、ひいては人事のDXを実現に効果的ですので、ぜひご検討ください。
※ベネワン・プラットフォームは、福利厚生サービス「ベネフィット・ステーション」を導入いただくと無料でご利用いただけます。
この記事のポイントは以下4点です。
この記事のまとめ
・リーンとは「ムダの改善」でトヨタ自動車の生産手法がその起源である
・シックスシグマとは「ムラの改善」で、本来は「100万個(回)のうちの不良(ミス)を3.4個(回)に抑えること」を意味し、不良を限りなく0に近づけることである
・リーンシックスシグマは改善根拠を可能な限り数値化された客観的データとしているため、改善において社員の合意を得やすい
・リーンシックスシグマとはムダとムラを改善し、安定して求める成果を出すことである
総合福利厚生サービス ベネフィット・ステーションとは?
ベネフィット・ステーションは、従業員満足度を向上し、健康経営やスキルアップを促進する総合型福利厚生サービスです。
グルメやレジャー、ショッピングだけでなくeラーニングや介護・引っ越しなどライフイベントに関わるものまで、幅広いメニューを取りそろえています。
さらに
・Netflixが見放題のプラン
・お得な特典や割引がついたサービスを会員企業の従業員様が給与天引きでご利用頂ける、給与天引き決済サービス
などをご用意しています。